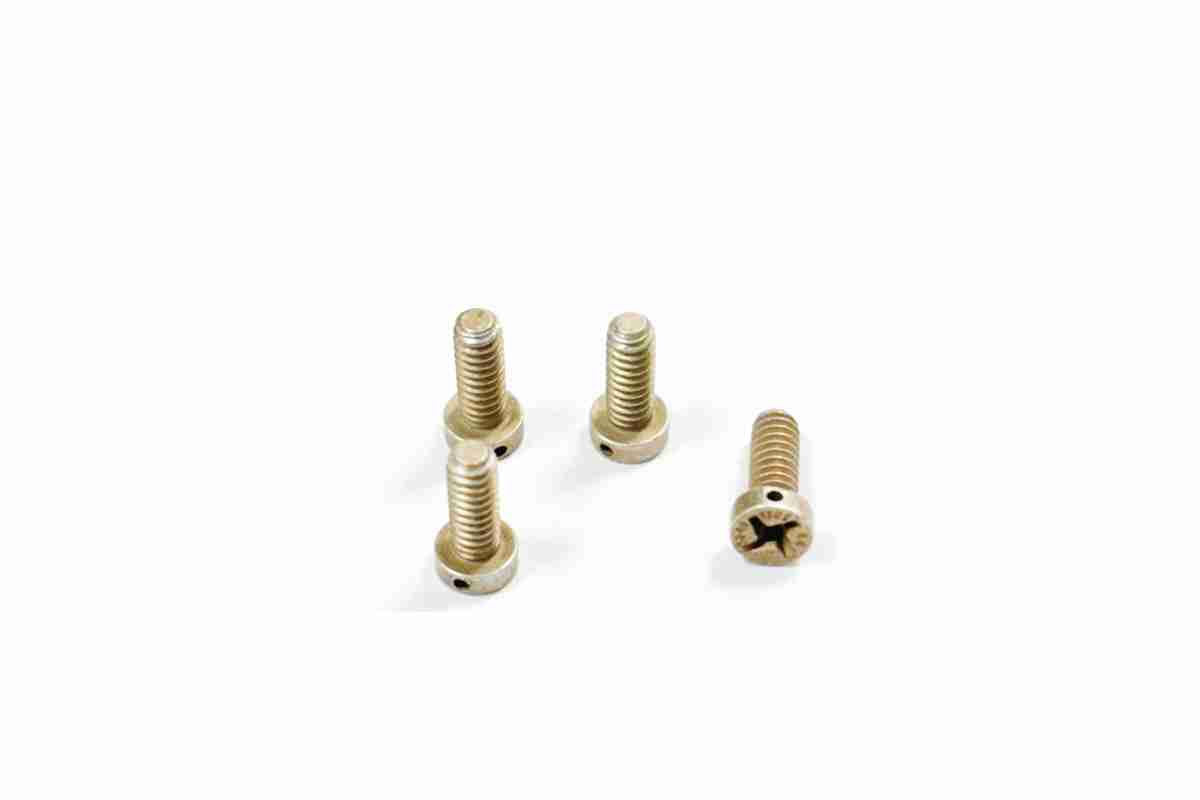
Fasteners are ubiquitous elements in hundreds of industries, such as construction, the automotive world, aerospace, and renewable energy. For a fasteners company in India, the choice of raw material directly impacts performance, reliability, and long-term usability. This article focuses on commonly used fastener materials—stainless steel, titanium, and high-temperature alloys—that can help one choose correctly based on particular requirements.
Properties of Fastener Materials
Material properties play a crucial role in deciding the suitability of fasteners, especially for a fasteners company in India catering to diverse environmental and mechanical demands. Important factors include strength, durability, corrosion resistance, and thermal stability, which ensure optimal performance in specific applications.
- Strength: Material’s ability to withstand mechanical stresses without deformation or failure
- Durability: Long-term performance against wear, pressure, and environmental exposure.
- Corrosion Resistance: An important factor when fasteners are exposed to moisture, chemicals, or saltwater environments.
- Thermal Stability: The resistance to maintaining mechanical integrity under high or fluctuating temperatures.
These properties ensure that the fasteners work as needed in their applications.
Popular Fastener Materials Overview
-
Stainless Steel
Stainless steel fasteners are one of the most useful and used materials because of the following reason:
- Corrosion Resistance: It has great anti corrosive and oxidation which makes it ideal for external, marine and chemical use.
- Strength & Flexibility: Stainless Steel fasteners are utilized in the colossal construction, automobile and heavy machinery industries.
Grades:
- 304 Stainless Steel: a general-purpose option appropriate for most of the applications.
- 316 Stainless Steel: More corrosion resistant than the above and is used in marine and industrial applications.
This strength and resilience make stainless steel a go-to choice for any project that requires reliability and durability.
-
Titanium
Titanium fasteners are valued for their performance in high-stress applications:
- Lightweight Strength: Titanium possesses the best strength-to-weight ratio. It is extremely useful for aerospace and medical applications.
- Corrosion Resistance: Resistant to seawater, chlorine, and many aggressive chemicals, titanium fasteners are ideal for extreme environments.
- High Temperature Tolerance: Titanium can maintain its properties even at high temperatures, thus suitable for jet engines and automotive exhaust systems.
Titanium is costlier than other materials; however, the special benefits it provides give value for its application in high-stakes conditions.
-
High-Temperature Alloys
High-temperature alloys such as Inconel and A286 are essential in extreme applications:
- Inconel: Due to high strength, it resists oxidation much better than other materials; hence used in turbines, power plants, and high-performance engines
- A286: High tensile strength alloy, widely used corrosion resistant material in the aerospace and petrochemical industry
- Nimonic Alloys: They have been developed for long time durability at high temperature applications like power generation and automotive exhaust systems.
These materials give a great amount of structural integrity and reliability in markets that require peak performance.
Specialized Materials for Niche Applications
For unique requirements or niches, specialized materials provide niche solutions:
- Low Carbon Steel: Offers very good formability and weldability, usually used in building and general manufacturing.
- Specialty Alloys: Developed for specific purposes, such as, surgical implants, novelties or applications within the renewable energy spectrum with excellent mechanical strengths coupled with decent corrosion resistance properties.
- Bearing Steel: This has an industrial and mechanical application by virtue of its strength and quality of durability.
These products will be suitable for certain industrial applications with special problems. They will work for peak performance.
Factors Affecting the Choice of Materials
Selection of material depends upon many factors:
- Environmental Factors:
Presence of Corroding Agents: In marine or chemical environments, then stainless steel or titanium fasteners would be used.
High Temperature: For very high temperature or highly variable temperatures, high-temperature alloys would be used for those applications.
Load and Stress: Applications which have high load or stresses demand superior tensile strength material, which can be titanium or Inconel.
- Cost vs. Performance:
Low-carbon steel is cost-effective and suitable for generalized applications; however, titanium, for example, is suitable when a stable engineered product is needed.
- Regulatory Requirements:
However in the case of aerospace and defense industries, there is a great effort made to ensure that higher standards are observed. So in these cases, specialty alloys or options that meet the DFAR requirements are very important.
Testing and Quality Assurance for Material Performance
Quality assurance is of significant value to ensure the performance and reliability of fasteners. Testing includes:
- Tensile Strength: It tests the ability of the material to resist stress without breaking.
- Corrosion Resistance: Salt spray or environmental exposure tests are performed.
- Hardness: It measures the material’s resistance to deformation under pressure.
- Metallurgical Analysis: This will help in ensuring consistency of the material composition and its structural properties.
- Advanced inspection processes such as optical sorting and magnetic particle inspection help to further control the quality of the products so that there is little risk of failure in critical applications.
In Summary
Any project’s success and safety largely depend on the fastener material chosen. Stainless steel, titanium, and high-temperature alloys are suited to specific needs, offering benefits ranging from corrosion resistance and lightweight strength to the durability required in extreme conditions. Careful analysis of environmental factors, mechanical demands, and regulatory requirements leads to the choice of material which optimizes performance and costs. For specific or critical applications, consult experts.