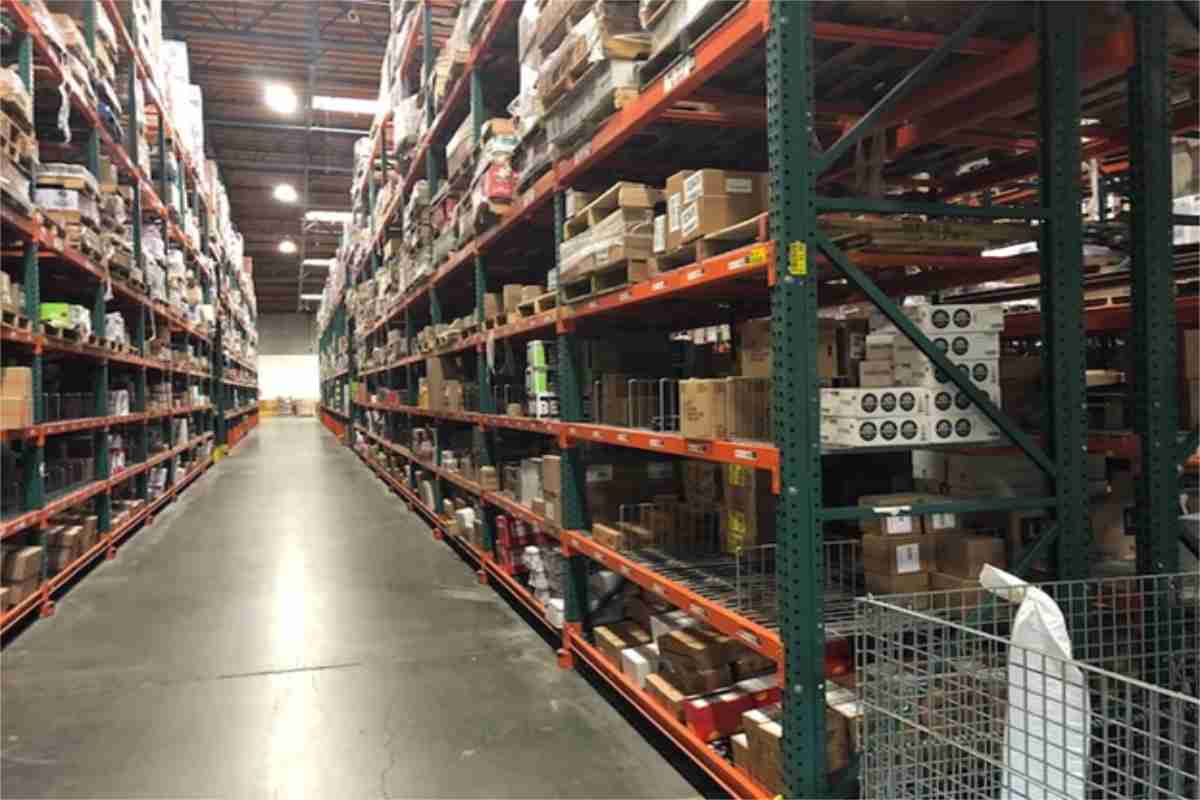
Warehouse racking is specifically designed to maximize space and improve the organization of storage solutions in a warehouse. Warehouse racking also includes shelf-like structures in tiers that hold goods orderly for easy retrieval and control of stock levels. They also include pallet racking, cantilever racking, and shelving systems ideal for different storage areas.
This improves the productivity of those operations by making certain processes more efficient and allows businesses to control their stocks in ever-changing logistics settings better. In this post, we cover ten key factors that, when considered, will enable you to choose warehouse racking that will work for your storage requirements and optimize your operations.
What are your Loading Capacity Parameters?
Before you search for warehouse racking for sale, It is critical to determine the parameters of the loading needs of your warehouse facilities. Even if each of the racks cannot withstand the weight of the goods within them, each of the shelves would not damage the structure of the racking system. It is mandatory to check on the weight that is likely to rest on individual shelves and the loading capacity of the system as a whole. This will help with the right usage of the equipment. Being strategic will also help with the prevention of accidents, in addition to prolonging the time of the racking system.
Physical Location And Space Available
Racks are always the most important part of storing goods; however, when selecting a rack, examine the measurements of the warehouse, including space and entities like the ceiling. It is critical to optimize vertical and horizontal use of space so that the warehousing density is high. However, ensure the final solution is deliverable, respecting distance and space requirements for aisles and equipment usage. Space analysis performs that function, which reduces bottlenecks and thus improves operational efficiency.
Items Or Products To Be Held In A WareHouse
The products that must be stored and their types, size, and shape determine the racks to be installed. For instance, a pallet racking system would be best for storing mass-produced goods, and tangential racks would be best for storing irregularly shaped and long items. Assure that you are knowledgeable about the kind of goods in your original inventory so that you can efficiently choose a suitable fitting system to handle the goods appropriately. This element is essential in determining the products’ good quality.
Space And Easy Access To The Goods And Retrieval Of Goods
Operational efficiency is determined by the ease of accessibility to items well kept in their containers or boxes. If the cost of maintaining the inventory is high, then the type of system implemented, whether selective or direct, will have to provide that feature. The necessary fabrication is determined, supporting the two aspects, based on the arms’ storage capacity and the speed of retrieving the item considering the operational aspect.
Durability and Material
How the racking system is constructed determines how strong and resilient it will be to wear and tear. Steel is quite a popular option due to its durability and strength. However, environmental factors, such as moisture, would mean that galvanized or powder-coated racks are needed to reduce the risk of rusting. Good quality materials guarantee that the system will last for everyday use over time while remaining safe.
Scalability and Flexibility
A racking system that is scalable and flexible is needed to accommodate future expansion or alteration in storage requirements. Easy expansion and reconfiguration while incurring minimal costs is possible with modular systems. Such flexibility allows one to conserve money and resources from a longer perspective, making the warehouse racking worthwhile.
Compliance with Safety Standards
Following the basic local safety regulations and industry requirements is essential during the selection of racking. This comprises labeling of racking load capacity, proper anchoring, and routine checks. If not complied with, they could result in accidents, fines, or even suspension of operations. Safety personnel may mitigate these factors to ensure that the racking system satisfies all of the required criteria protecting the workers and stock.
Budget limitations
The budget is one of the factors that determines what type of racks you can afford. While cheap options might be tempting, sacrificing quality usually means replacing them often or sometimes unsafely using them. Make an educated investment by examining the overall cost of ownership, including integration, maintenance, and updates that might be needed in the future.
Equipment Harmony
Pay attention to the racking configuration of the mechanical lifts, pallet jacks, and/or automatic systems deployed in the warehouse. When equipment is not properly configured, it can cause a waste of time or, even worse, damage to the racks. To ensure the smooth function of activities while minimizing disturbances, check the specs of the equipment about the system in use, such as its aisle width, height, and the load it can carry.
Handling of the system
Employing professionals for the installation process is extremely necessary, lest the system is not calibrated properly and, most importantly, safely during installation. Positioning and anchoring the racks poorly risks decanting and, hence, accidents. Also, think of how much maintenance your selected system will require. Designs that are quick and easy to maintain minimize idle time and maximize the lifespan of the racking, making it a winning solution in the long run.
Conclusion
When selecting a warehouse racking system, it is important to assess various factors such as weight and volume capacity, amount of space, accessibility, and others. Keeping these ten issues in mind helps reach decisions that are good in terms of space utilization and improvement of operational processes. Make sure you have a plan that will guarantee a system that is safe, long-lasting, and adjustable to the needs of your particular warehouse.